Introduction
The nebulizer is a critical component of your ICP sample introduction system, so why not opt for the highest quality? Glass Expansion has been manufacturing ICP nebulizers since the early 1980s and continually updates nebulizer designs to improve performance and ease of use. Whether your ICP laboratory is analyzing clean aqueous samples, samples containing HF and/or high dissolved salts, or volatile organic solvents; Glass Expansion has a nebulizer to suit your needs.
Sample Uptake Rate
Sample is delivered to the nebulizer of the sample introduction system typically via a peristaltic pump. The operator chooses the appropriate pump tubing internal diameter and pump speed to achieve the desired sample flow rate. This is typically between 1 and 2 mL/min for ICP-OES and somewhat lower for ICP-MS. In order to achieve the best analytical performance, sample delivery must be consistent over both the short and long term. Failure to consistently deliver sample shows up in terms of poor precision and inaccuracy but may not become evident until a QC sample is measured. The potential causes of this failure are as follows:
- Worn pump tubing; as the pump tubing wears its compressibility degrades and the sample uptake rate slows and becomes inconsistent.
- Incorrectly adjusted pressure on the tubing clamp; a peristaltic pump includes a clamp that places a variable pressure on the tubing that is wrapped around the rollers. This optimum pressure is that which is high enough to completely close the tubing when it is between the clamp and roller but not so high that it will shorten the lifetime of the tubing.
- Worn pump rollers; as a peristaltic pump is used the rollers may with time develop a low spot. A low spot on any roller will cause erratic sample delivery.
- Clogged nebulizer; when the sample line of a nebulizer becomes clogged either from an errant particle or salt build up, it produces significant back pressure and reduces the sample uptake rate.

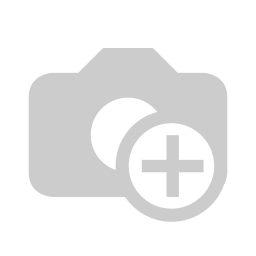
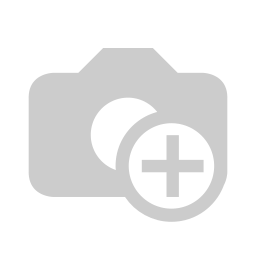
A sample uptake monitor is now available that can measure and record the sample uptake in real time and display the value both digitally and graphically. Known commercially as the TruFlo™ (Glass Expansion, Melbourne, Australia), the device uses a thermoelectric sensor to cover the range of 0.05 to 4.0 mL/min (Figure 2). The TruFlo tells the operator instantaneously when the sample uptake rate deviates significantly from the desired level. In fact, a range can be programmed so that an alarm is triggered when the sample uptake falls outside the range (Figure 3). Figure 4 shows the effect of pump clamp tension on signal. Note that there is an optimum tension for maximum flow and minimum pump noise. Additional tension will only prematurely wear the tubing and may even produce a lower sample flow. Figure 5 plots the relationship between pump speed and sample uptake rate. As expected, pump speed is proportional to uptake rate.
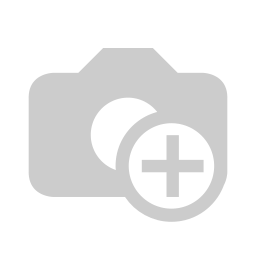
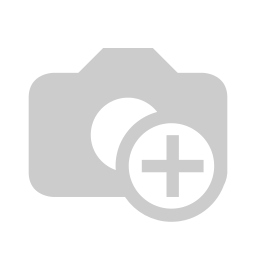
and sample flow rate.
Spray Chamber Temperature
The temperature of the spray chamber in an ICP spectrometer has a direct influence on the sample transport and the signal stability. However, even though the detectors are thermally controlled, the spray chamber temperature (in many cases) is incorrectly assumed to be constant. The importance of spray chamber temperature control is more accepted for ICP-MS for two reasons. First, optimizing both the spray chamber temperature and the nebulizer gas flow allows oxide interferences to be minimized. Also, stabilizing the spray chamber temperature for an ICP-MS is generally accepted to significantly improve precision. Historically, the application of a controlled temperature spray chamber for ICP-OES has been restricted to reducing the plasma load when analyzing volatile solvents. It is likely that this restriction is due to the complexity and expense of adding a temperature-controlled spray chamber. Traditionally, this involved the acquisition and installation of an external chiller in combination with a jacketed spray chamber (Figure 6). Recently, a free-standing Peltier driven device has been introduced which significantly simplifies temperature control. The IsoMist™ Programmable Temperature Spray Chamber (Glass Expansion, Melbourne, Australia), also shown in Figure 6, has a range of -10 to 60°C in 1°C increment and a stability of +/- 0.1°C.
The applications of a temperature-controlled spray chamber are diverse and have been described elsewhere. From a quality control viewpoint, the ability to both control and monitor the spray chamber temperature provides an added layer of confidence in the analytical results. Figure 7 demonstrates the signal drift of an ICP-OES system with and without temperature control. Note that the drift range has been reduced from 6% to less than 1%. The benefit of this improvement comes into play in a number of applications. For environmental analyses, the added stability means reducing QC failures and decreasing the number of standardizations. For precious metal assays, it means higher accuracy, which translates into higher profits. With the IsoMist, a plot of measured temperature vs. time can be displayed and saved as a record of performance during the sample run (Figure 8).
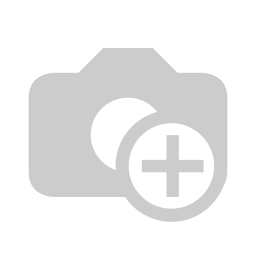
Optimization of the sample mass transport is another advantage to controlling the temperature of the spray chamber. Figure 9 shows the effect of spray chamber temperature on ICP-OES signal for a wide range of element lines. Note the large and varied effect of temperature on the individual lines selected. In the most dramatic case (Ca317.9), 1°C results in a 5% change in signal, while in the least dramatic case (Al396.1), 1°C causes only a 2.4% change in signal. The conclusions are threefold as follows:
- Spray chamber temperature is a critical parameter.
- Due to the varied effect of temperature, internal standardization may not be an accurate means of compensation.
- To achieve the best detection limits, the instrument should
be operated at the maximum mass transport that will sustain
a robust plasma.
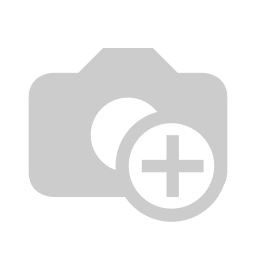
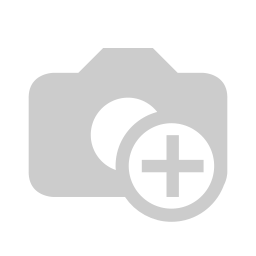
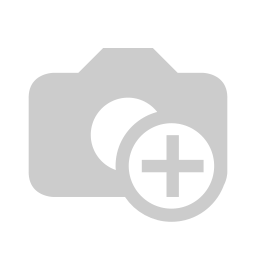
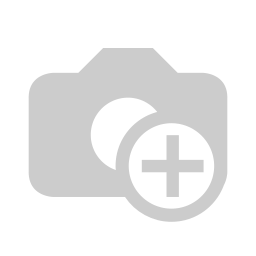
Summary
The control of two additional parameters adds even more credibility and robustness to ICP spectrometry as an analytical tool. Figure 10 illustrates the ICP-MS system showing the positioning of both the TruFlo and IsoMist. Both sample flow rate and spray chamber temperature have profound effects on the performance of this technique. In the first instance, a sample flow monitor assures the operator of acceptable performance and provides a digital graph of the performance over the length of the sample run. In the second case, a programmable temperature spray chamber not only monitors but controls the temperature of the spray chamber to achieve optimum, consistent, and reproducible performance.
References
- H. P. Longerich and W. Diegor, J. Anal. At. Spectrom. 16, 1196-1201 (2001).
- M. G. A. Korn, D. S. S. dos Santos, B. Welz, M. G. R. Vale, A. P. Teixeira, D. C. Lima, and S. L. C. Ferreira, Talanta 73 (1), 1-11 (2007).
- S. J. Hill, J. Hartley, and L. Ebdon, J. Anal. At. Spectrom. 7, 23-28 (1992).
- A. S. Al-Ammar, R. K. Gupta, and R. M. Barnes, J. Anal. At. Spectrom. 14, 793-799 (1999)
- J. Dulude, R. Stux, and V. Dolic, Pittcon, Paper #1370 (2007)