Introduction
Radio Frequency (RF) alternating current has been used for quite some time to induce a heat source in a localized region. Development started in the 1960’s with the first commercial ICP available in 1974.1 Originally the RF alternating current was generated by a valve or power amplifier tube, which was connected to the RF load coil via a matching circuit. This matching circuit was generally made up of a fixed capacitor and a tuning or variable capacitor. This tuning capacitor was adjusted to balance the system and lower the reflected power back to the RF generator. Today many if not all use a solid-state RF generator and amplifier; some have matching circuits and others allow the frequency to change to match the plasma load (free-running generators). All but one of the ICP instruments use a coil to generate the plasma inside a torch. The coil is designed to match the rest of the RF system.
RF Coil Plating
So why are some RF load coils plated? This goes back a long way to when the purity of copper was not as high as it is now. Silver plating of load coils was found to give higher conductivity of the RF energy. Once the purity of copper increased it was shown that the conductivity of the copper load coil was better than the silver-plated coil.
So why are most RF load coils still plated? The answer is a little more complex.
The ICP’s of today use two RF frequencies 40 and 27 Mhz to generate the plasma. For these two frequencies, the majority of the current will flow in the outer 10-13 micron layer for copper and silver and 12-15 micron for gold.
The environment inside the torch box can be highly corrosive, and bare copper will corrode faster leading to a buildup on the outside of the coil which will lower the conductivity of the coil. It will also make the surface of the coil uneven, meaning the current has to travel a larger distance which increases the resistance of the coil. Plating the coil with a very high-purity silver gives better corrosion resistance, as silver oxide does not affect the resistance. However, silver is attacked by sulphides, which leads to a buildup on the silver surface. Alternatively, gold can be used to provide better corrosion resistance. However, there are a couple of issues with gold in an RF system. Firstly the conductivity of pure gold is only around 75% that of pure copper, and secondly, the thickness of the layer of gold plating required to give a non-porous layer would mean that the majority of the current will flow through the gold-plated layer. This lowers the conductivity of the coil. For this reason, a thinner layer is typically used which is not thick enough to stop the porosity; hence the gold-plated coils will eventually corrode. The addition of a PTFE coating over the silver coating will give very good corrosion resistance without the increase in resistance. However, the constant heating and cooling in the torch box does eventually lead to the breaking down of the PTFE coating and exposes the silver-plated coil to the atmosphere in the torch box.
There are a couple of other important factors in the plating process that will have major effects on the conductivity of the coil. Firstly, the purity of the metal used for plating, and secondly how these layers are applied. There are very few platers that use high-purity gold and high-purity silver. Most use a brightener in the solution so the end product has a shiny finish without the need to polish. A pure silver or gold plated finish will be dull in appearance (there are a number of coils now available from OEMs that have a dull silver finish). The coils Glass Expansion provides all use high-purity gold and silver and are all physically polished after plating to give the smoothest finish to the outside of the coil reducing resistance. A side benefit is the enhanced visual appeal of a bright and shiny finish. The more important aspect of plating is how it is applied and what is done to the coils during the process. The proprietary process used by Glass Expansion ensures the plating has the highest uniformity and purity.
Energy Transfer from the Coil
The RF coil is the last component in the RF system of your ICP-OES and ICP-MS that is used to generate plasma. Therefore, the condition and shape of the RF coil can have a major effect on the efficiency of transferring energy to the plasma.
Being exposed to the environment of the torch box, the RF coil is susceptible to corrosion. The greater the corrosion, the larger amount of energy is needed to produce a plasma of the same power. This transfers undue stress on the rest of the electrical components used in the RF system of your ICP-OES and ICP-MS, possibly contributing to premature failure.
Older ICP’s used a power amplifier (PA) tube as part of the RF system. Excessive stress on this component would result in a service call of several thousand dollars. Newer ICP’s utilize a solid-state RF system which, although more modular, would result in an even more expensive service call to replace. Regular replacement of your RF coil reduces the load on the RF generating system and ensures your ICP is running optimally. The suggested rate at which you should replace your RF coil is every 6 months for ICP-MS and every 2 years for ICP-OES. Depending on the laboratory environment your instrument may require more or less frequent replacement. The RF coils pictured in Figure 1 are well past the point of replacement. Coils in this condition increase the stress applied to other components in the RF generating system and can shorten the lifetime of your torch, in addition to the power amplifier or solid-state generator.
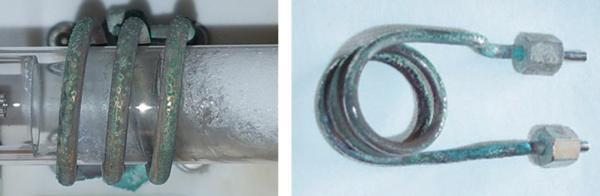
There are three factors affecting the transfer of energy from the RF coil:
- Concentricity and alignment - are very important in producing a correctly shaped plasma, which consistently needs to be located in the same position.
- Correct dimensions - being part of the RF system, the coil dimensions are also important in the tuning of the circuit. Slight changes in dimensions can produce small changes in resistance or inductance. These changes can also lead to variations in the shape of the plasma and affect energy transfer from the plasma to the sample.
- Base metal/plating - the most efficient conductor of RF energy is pure silver followed by annealed copper. There is very little difference in the conductivity of these materials but there is a great deal of difference in cost. Copper is used as the base material of all commercially available coils but different manufacturers use different plating materials. Silver has the best conductance and gold has the best corrosion resistance.
The next step is to transfer the energy from the plasma to the aerosol sample. There are two main factors that affect this transfer:
- Argon gas flow rates and quality. Obviously, high-purity argon is required and is generally available although it can be quite expensive, especially in some countries. Higher nebulizer argon flow rates will shorten aerosol residence time and can also cool the plasma, both of which lead to lower intensities.
- The torch containing the plasma. The torch needs to be concentric and of the highest quality quartz. If the outer tube becomes devitrified, the transfer of energy is restricted due to losses incurred by heating on the surface of the outer tube, thereby reducing the available energy for the atoms and ions.
Why Choose a Glass Expansion Coil?
Glass Expansion coils are produced from the highest quality and purity raw materials and plated using proprietary methods to obtain maximum RF transmission efficiency. Examples of copper, gold and silver Glass Expansion RF coils to suit the Agilent 7900 ICP-MS are shown in Figure 2.
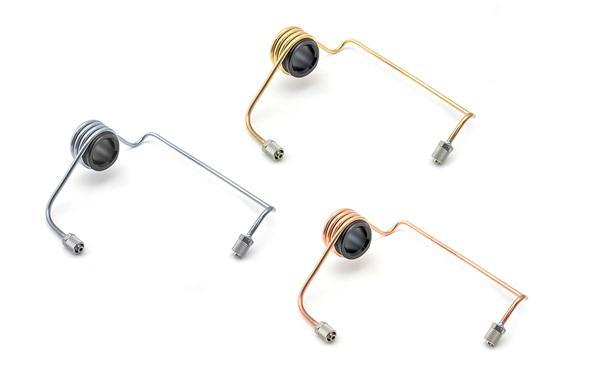
Advantages of Glass Expansion RF Coils:
- High purity and consistent plating promote extended coil life
Each coil is supplied on a plastic former ensuring correct dimensions are maintained and allowing easier installation. These formers can be then used periodically to check the coil dimensions, so it is a good idea to keep the former even after coil installation. - Each coil is supplied in a special protective container to ensure correct dimensions are maintained, and the coil arrives corrosion free.
- Correct alignment of the coil with respect to the torch body reduces devitrification of the outer tube and ensures the plasma is concentric within the torch allowing the sample aerosol to travel correctly through the plasma.
In addition to producing the highest quality RF coils, Glass Expansion also simplifies the installation with a “Do-it-yourself” RF coil installation kit. Each kit is designed specific to the ICP model, including an installation tool, spanner and easy-to-follow step-by-step instructions. This way you ensure proper alignment and concentricity each and every time, in addition to saving the cost of a service call and minimizing ICP downtime. Glass Expansion has recently added to its family of RF coils to accommodate more models of ICP-OES and ICP-MS instruments.
References
- Practical Guide to ICP-MS, Third Edition, CRC Press, 2013, Robert Thomas
- Radio Frequency Performance of Electroplated Finishes, Proceedings of the Institute of Radio and Electronics Engineering 1970, Alan. M. Fowler.